A peek into decarbonization efforts in steel and cement production, next-gen hydrogen technologies and supercapacitors, and more
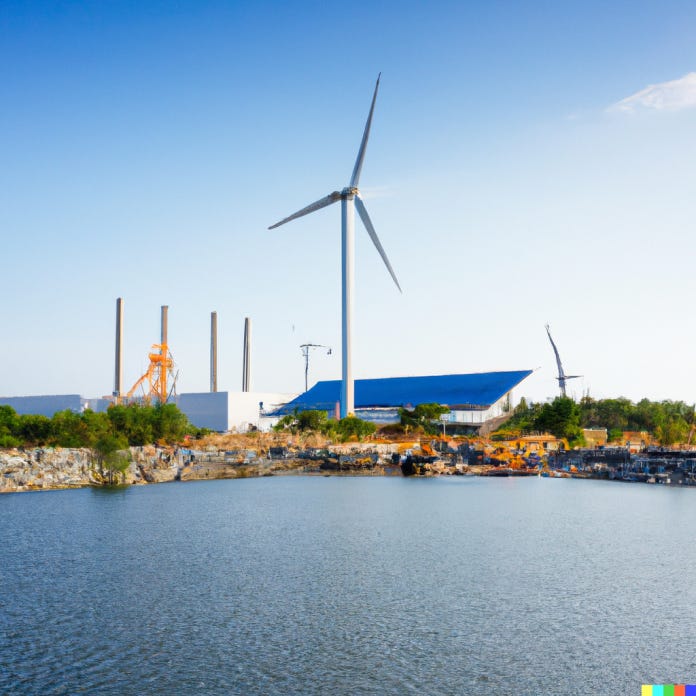
Content from TechSprouts
- Deep Dive Article: Synthetic Biology: Changing the way you eat your food!
Synthetic biology is transforming the food industry, enabling the production of complex food products and ingredients that are safer, nutritious, delicious, and more sustainable than the existing alternatives. The sector has seen significant investments and growth, and India has the potential to emerge as a global supplier of high quality biotech based food products. - External Collaboration with Biospectrum India: How Early Diagnostic Tech Can Stop Cancer In Its Tracks
Surviving any form of cancer is challenging. It is more challenging if detected in the later stages. Data suggests that average 5-year survival of patients who were detected with cancer at an early stage was 91 per cent which dropped to 26 per cent at late stages. Therefore early detection of cancer can go a long way in saving patient lives.
Deep Science funding updates
- CrisprBits raised a pre-seed round of $0.25 million from US-based VJ Group for developing its CRISPR-based point of care diagnostics platform.
- Mindgrove Technologies which develops cost-effective and power-efficient system-on-chips (SoCs) raised a seed funding of $2.325 million led by Sequoia Capital along with Speciale Invest and Whiteboard Capital.
- Enzene Biosciences, which is developing biosimilars, novel biologics, synthetic peptides and phytopharmaceuticals, raised $50 million from its parent company Alkem Laboratories along with Eight Road Ventures and F-Prime Capital to boost its manufacturing footprint.
Deep science ecosystem updates
- Samsung Semiconductor India Research (SSIR) and the Indian Institute of Science (IISc) have collaborated to drive R&D in the field of on-chip Electrostatic Discharge (ESD) protection which is one of the main reasons for Integrated Circuit (IC) failures.
- University of Ladakh has collaborated with the Indian Institute of Chemical Technology (IICT)-CSIR to extract and isolate high-altitude medicinal plants.
- Centre for Cellular and Molecular Platforms (C-CAMP) launched the National Diagnostics Catapult (C-CAMP InDx 2.0) to boost the infectious disease diagnostics space in India.
- The Department of Science and Technology (DST) and Fraunhofer Institute for Solar Energy Systems (Fraunhofer ISE) signed an LOI for a long-term collaboration on developing next generation hydrogen technologies.
News from the research community
- Researchers from SMITA (Smart and Innovative Textile Materials) Research Lab, Department of Textile & Fibre Engineering, IIT Delhi along with a team from AIIMS Delhi, Department of Ophthalmology have developed a biopolymer scaffold, Polycaprolactone (PCL), as an alternative to HAM (Human Amniotic Membrane) for patients with limbal stem cell deficiency.
- Researchers from the International Advanced Research Centre for Powder Metallurgy and New Materials (ARCI) along with the Indian Institute of Technology, Hyderabad (IITH) have developed a high capacity, cost effective supercapacitor system with 2.2 V-wide electrochemical window and 83% energy retention after 10,000 charge-discharge cycles.
Deep Science Thoughts
Decarbonizing Cement and Steel
Cement and steel together form a critical component of our modern industrial economy. However, they are also extremely resource-intensive. Together, the cement and steel industries produce roughly 14% of our global GHG emissions. They are expected to grow further by 3–5% each year, too. This makes it critical to find ways to decarbonize the processes involved in producing steel and cement.
The most carbon-intensive steps in steelmaking are the production of coke and the reduction of iron ore in a blast furnace. Cement, on the other hand, produces carbon emissions both directly (from the heating of limestone to generate lime) and indirectly (from the burning of fossil fuels to fire the kiln). Decarbonizing these processes at scale, while maintaining price competitiveness with legacy processes, is incredibly challenging.
There are a number of low-intervention improvements that can be made for incremental decarbonization. For steel, two such improvements are utilizing waste heat and improving overall efficiency. Similar interventions exist for cement, such as switching to composites like Pozzolan Portland Cement (PPC). However, such improvements have limited use, as they can only reduce the total emissions by 10–20%.
Carbon capture offers great promise–this involves chemically or physically capturing the carbon dioxide released during the fuel-burning process. For cement production, in fact, carbon capture is the primary path to decarbonization. More work on the technology is needed both to reduce the cost as well as make the process more efficient in terms of capturing all the CO2 emissions. Market entry for widespread adoption of carbon capture techniques in cement production is expected only in the following decade, leaving innovators and entrepreneurs with a wide space to operate in.
Aside from carbon capture, there is a wide variety of innovative approaches being undertaken to decarbonize cement production. These range from using alternate materials and fuels to incorporating biological systems and microorganisms. For example, US-based Brimstone has developed a new process to source lime from calcium silicate instead of limestone, reducing the intrinsic carbon emissions from the clinker-production process. Companies like Prometheus Materials and BioZeroc are using algae and bacteria to generate zero-carbon cement.
With regards to steel, huge efforts have focused on incorporating green hydrogen as a fuel to convert iron ore to metallic iron. This has followed decades of research and development work in the direct reduction (DRI) process as well as in electric arc furnaces (EAF). Technologically speaking, the process of using hydrogen in place of coal or natural gas for steel production is well known now. However, the current price of green hydrogen is too high for zero-carbon, or green, steel to be cost-competitive. Thus, the adoption of green steel hinges on technological innovations at scale in the green hydrogen manufacturing process.
Many European steel manufacturers are leading the way when it comes to green steel production–H2 Green Steel is set to lead the way with its carbon neutral steel plant in Boden, Sweden, to open in 2025. Other large steel players are entering the green steel industry too, such as Thyssenkrupp who is investing $1.9 billion in a hydrogen-powered reduction system to create high-quality steel with the aim of producing 2.5 million tons of low-carbon steel by 2026. ArcelorMittal will be producing 1.6 million tons of zero-carbon steel a year by 2025 at a new plant in Spain.
However, hydrogen is not the end-all and do-all of green steel approaches. There are a number of alternate approaches in the works too. For example, USA-based Boston Metal has developed a process called molten oxide electrolysis, wherein the iron ore is reduced to metallic ore directly via the application of electricity. ArcelorMittal has partnered with synthetic biology company LanzaTech to develop a technology called Carbalyst, where carbon-rich waste gases are captured and upcycled into recycled chemicals and fuels.
To summarize–reducing the GHG emissions of the cement and steel industries is a huge and urgent task. There are a number of technological approaches which are at different stages of readiness, whose applicability will vary across economies and geographies. Given that the complete decarbonization of these industries is going to be a multi-decade effort, it also provides an opportunity for researchers, entrepreneurs and multinationals to contribute to and capitalize on.